Advanced NDT
What is advanced Non destructive testing?
FALCON Inspection & Services offers you the most effective non-destructive testing (advanced ndt) for a diverse range of industries and ensures the reliability and safety of your products, equipment or installations by detecting defects before they cause serious damage and guaranteeing compliance with international standards.
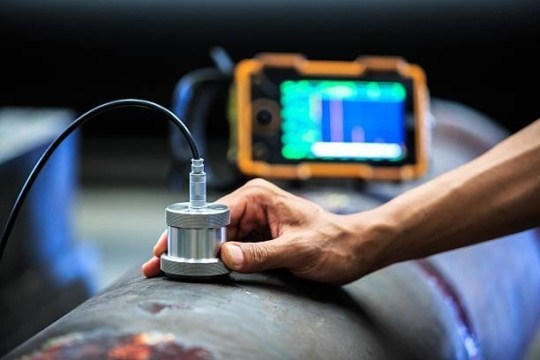
Advanced NDT Services
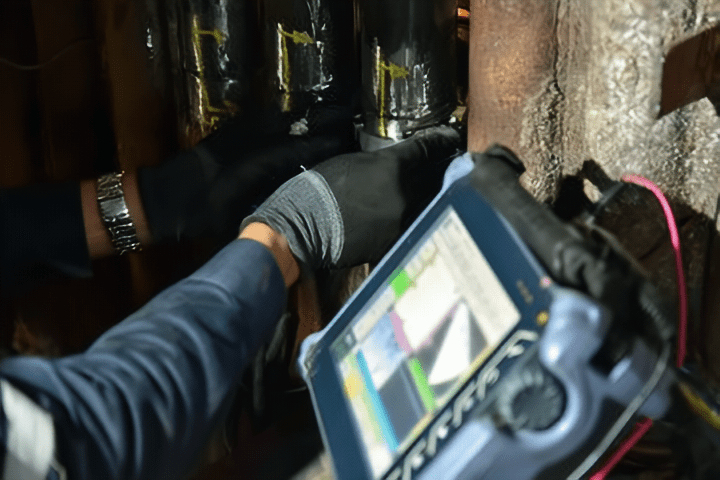
Phased Array Inspection (PAUT)
PAUT, also known as phased array ultrasonic testing, is an advanced NDT inspection technology that employs a series of ultrasonic testing (UT) probes made up of several tiny elements. To create the phased part of the process, each of them is pulsed individually with computer-calculated timing, while the array refers to the numerous elements that make up a PAUT system.
Falcon Inspection & Services has ANST level 2 and level 3 experts who can help you with your PAUT requirements in Tunisia or internationally (europe , africa, middle east, aisa) .
- Improved portability of flaw detection
- Faster inspection
- Provides a permanent inspection record
- Safe for the user
- No dead zone
- Weld Inspections
- Thickness Measurements
- Corrosion Inspection
- Pressure Vessels
Alternating Current Field Measurement (ACFM) Inspection
An Alternating Current Field Measurement (ACFM) probe injects an electric current into a component in order to measure the electromagnetic fields around the surface of the material in order to look for flaws. Surface breaking-cracks in metal components are frequently identified and sized using this method.
Falcon Inspection & Services has inspectors trained on this advanced NDT method that can help you detect defects while reducing risks.
- Applicable for base material or welds, ferritic or non-ferritic conductive metals
- Can be used on hot surfaces, underwater, or in irradiated environments
- Provides both depth and length information
- Accurate sizing of defects up to 25mm in depth
- Requires minimal surface preparation and can be applied over paint and other coatings
- Applicable for underwater inspection as well as normal inspection
- Inspection data can be stored and analyzed offline
- Inspection can be encoded
Detection and sizing of fatigue cracks and hydrogen cracking
Inspection of fillet welds in mobile offshore drilling Units
Inspection of fillet welds in highway bridges
Inspection of rail components
Inspection of gear box, gear teeth, crank shafts, cylinder heads, turbines etc. in aerospace industries
Detection of cracks and corrosion in vessels, storage tanks and piping in oil and gas and power generation industries
Inspection of drilling tools
Inspection of various components in automotive industries
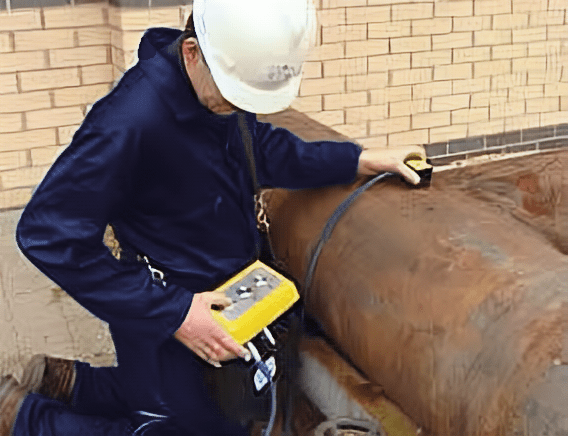
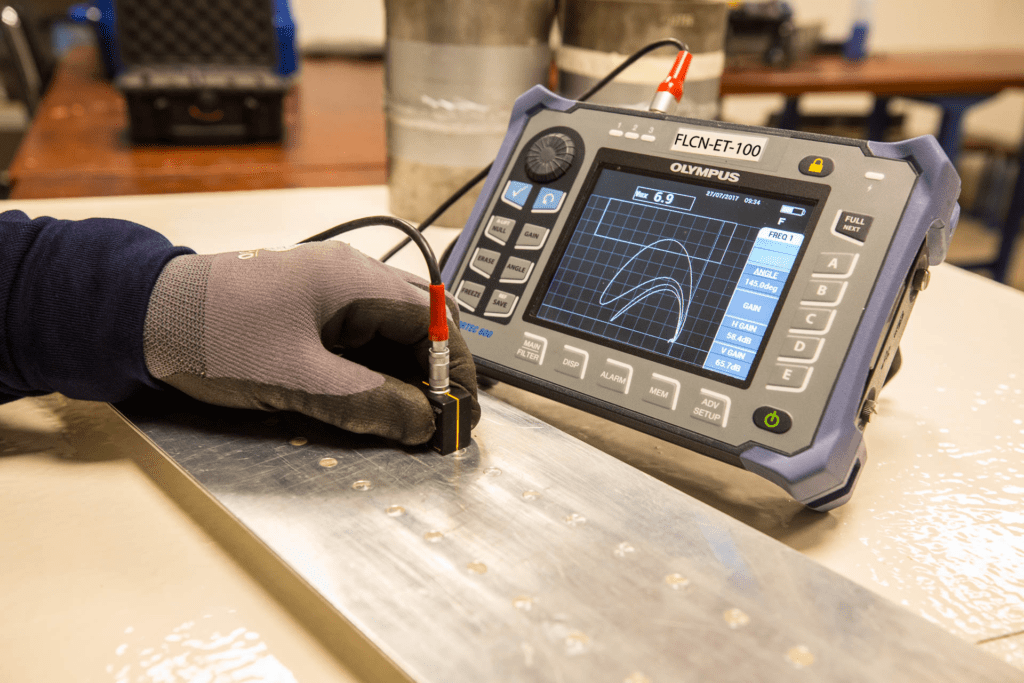
Eddy current Inspection (ET)
Eddy current testing(ET) is an advanced NDT inspection method that can be used to discover flaws, measure material, and coating thickness, identify materials and determine the heat treatment state of certain materials. This method uses coils to generate eddy currents in order to analyze the test piece.
Falcon Inspection & Services has trained technicians in ET inspection and can help you with your inspection requirements.
- Surface and near-surface fissures as tiny as 0.5mm can be detected, and defects can be detected across many layers, including non-conductive surface coatings, without interference from planar defects.
- Inspection of high-temperature surfaces and submerged surfaces using a non-contact approach.
- Test items with physically complicated geometries are effective.
- Gives you an immediate response
- Lightweight and portable equipment
- Quick setup time — no pre-cleaning is required, and no couplant is necessary to detect electrical conductivity of test objects
- Inspection of uniform parts such as wheels, boiler tubes, or aero-engine disks can be mechanized.
- Inspection of parts or components including:
Welded joints
Bores of in-service tubes
Bores of bolt holes
Metal tubes
Friction stir welds
Gas turbine blades
Nozzle welds in nuclear reactors
Hurricane propeller hubs
Cast iron bridges
Gas turbine blades
- Detection of defects including:
Surface-breaking defects
Linear defects (as small as 0.5mm deep and 5mm long)
Cracks
Lack of fusion
Generalised corrosion (particularly in the aircraft industry for the examination of aircraft skins) - Other applications
Identification of both ferrous and non-ferrous metals and with certain alloys – in particular the aluminium alloys
Establishing the heat treatment condition
Determining whether a coating is non-conductive
Heat treat verification of metals
Magnetic flux leakage (MFL)
Magnetic flux leakage (MFL) is an advanced NDT technique that uses magnets to detect corrosion, pitting and wall loss in steel structures.
In the petrochemical sector, magnetic flux leakage (MFL) is routinely used to inspect tank floors. Corrosion of the tank floor can result in product loss as well as environmental damage. As a result, tank floor inspections are critical in order to avoid such issues from occurring.
- One of the few methods used to inspect finned tubes ( NFT is also an alternative)
- Can be used on all ferromagnetic materials
- Good sensitivity to pitting
- High-speed inspection
- Corrosion detection in pipelines
- Corrosion detection in storage tank floors
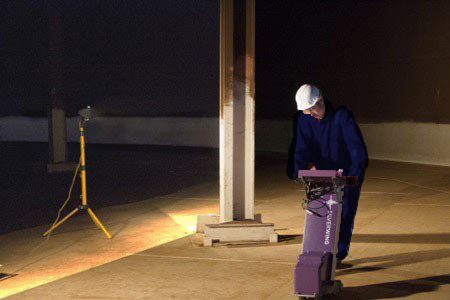
Digital Radiography (RT)
Digital radiography is a cutting-edge technique that uses digital detector devices to display an x-ray image on a computer screen without the need for developing chemicals or intermediary scanning.
A detector sensor converts the incident x-ray radiation into an equivalent electric charge, which is then transformed into a digital image.
Falcon Inspection & Services has also a radiographic film scanner and can help you digitize your films and extract useful data out of them.
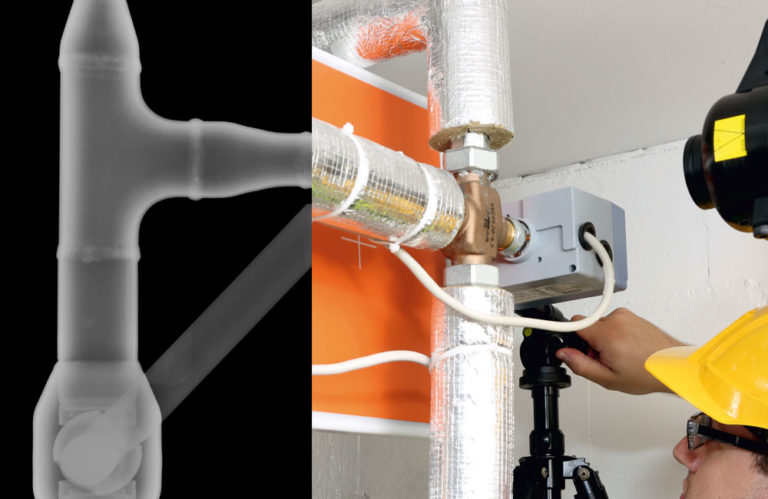
Do you need assistance with your NDE requirements ?
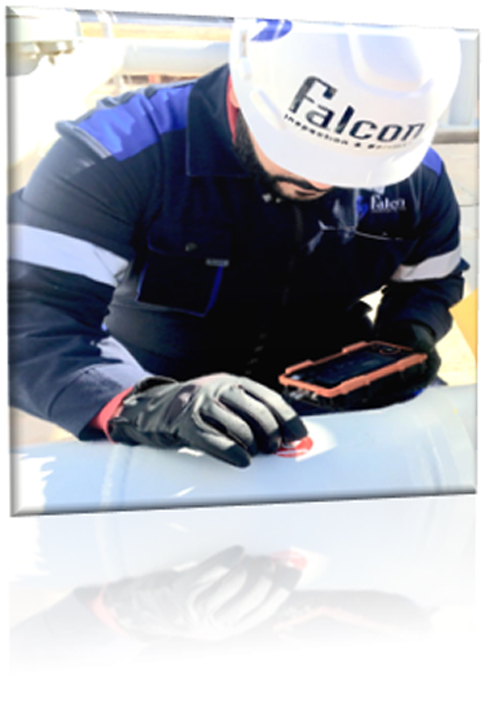
Falcon inspection & Services has a team of highly trained NDE level 2 inspectors and level 3 NDE experts that can help you with your non-destructive testing projects and requirements. Our team can validate your inspection procedures, perform NDE assessments and advise you with any non-destructive testing requirements you have.